Understanding Tube Connection Types
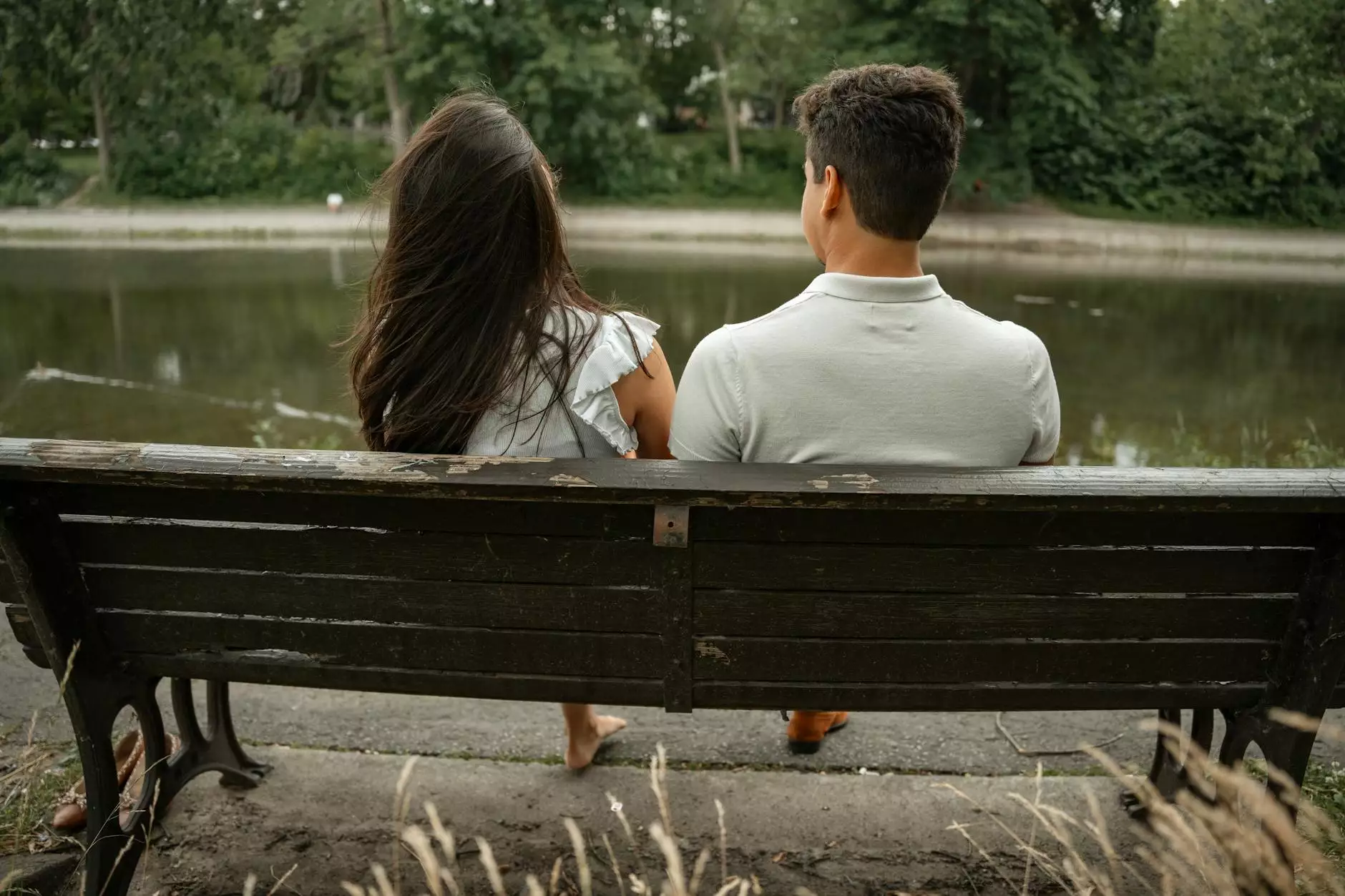
In the world of engineering and industrial applications, tube connection types play a crucial role in ensuring the efficiency and reliability of systems. Whether you are dealing with fluid transport, pneumatic systems, or various industrial applications, having a thorough understanding of these connections is essential. This article delves into the different types of tube connections, their specific features, and applications, to help you make informed choices for your projects.
What are Tube Connection Types?
Tube connection types refer to the various methods and fittings used to join tubes or pipes together. These connections are crucial in a multitude of industries including plumbing, hydraulics, and manufacturing. Different connection types provide distinct advantages depending on the specific requirements such as pressure handling, installation ease, and environmental factors. Let's explore some of the most common types:
1. Tube Fittings
Tube fittings are essential in the assembly of tube systems. They are designed to connect two or more tubes and facilitate the flow of fluids or gases. There are several kinds of tube fittings, including:
- Compression Fittings: These types of fittings use a ferrule to compress against the tube, creating a secure seal that prevents leaks.
- Flared Fittings: Here, the end of the tube is flared out to create a connection with another flared fitting, providing a robust and leak-free connection.
- Push-to-Connect Fittings: Also known as push-in fittings, these allow for quick assembly and disassembly without needing special tools.
2. Ferrule Fittings
Ferrule fittings are a specific type of tube connection that involves a ferrule, which is a ring that holds the tube in place and creates a tight seal. They are widely used for their reliability and effectiveness in high-pressure applications. The main types include:
- Single Ferrule Tube Fittings: These are the most commonly used ferrule fittings, featuring a single ferrule design that offers ease of assembly.
- Double Ferrule Tube Fittings: These fittings use two ferrules for enhanced sealing, making them ideal for critical applications where safety and reliability are paramount.
3. Forged Pipe Fittings
Forged pipe fittings are produced using a forging process, which involves shaping the metal under high pressure. This method results in a dense and sturdy fitting capable of withstanding high pressures and temperatures. Common types of forged fittings include:
- Elbows: Used to change the direction of the piping layout.
- Tees: Used to create a branch line in the pipeline.
- Couplings: Used to connect two pipes together.
4. Threaded Pipe Fittings
Threaded pipe fittings utilize male and female threads to create connections between pipes. They are easy to install and disassemble, making them ideal for a variety of applications. Key aspects include:
- Standard Taper Threads: These provide a leak-proof connection when tightened.
- Adapter Fittings: Used to connect mismatched threads or different pipe materials.
5. Flanges
Flanges are flat pieces of material used to connect pipes, valves, pumps, and other equipment to form a piping system. They provide a strong and leak-free connection. Types of flanges include:
- Weld Flanges: Designed for welding to the pipe.
- Slip-On Flanges: Easily fit over the pipe's end.
- Screw-on Flanges: Use threads to attach the flange to the pipe.
6. Valves
Valves are critical components in any piping system and come in various types to control the flow of liquids and gases. Notable valve types include:
- Check Valves: These allow fluid to flow in one direction while preventing backflow.
- Ball Valves: Characterized by a spherical disc that allows for quick shut-off.
- Needle Valves: Ideal for precise flow control.
- Manifold Valves: Used to control multiple flow lines in a system.
Choosing the Right Tube Connection Type
When selecting a tube connection type, consider factors such as:
- Pressure and Temperature Ratings: Ensure the fittings can handle the maximum pressure and temperature of your application.
- Material Compatibility: Choose fittings that are compatible with the fluids or gases being transported to prevent corrosion and leaks.
- Space Constraints: Some fittings require more space for installation, so understanding the layout is crucial.
- Ease of Installation: Consider the tools and time required for installation. Quick-connect fittings may save time and labor costs.
Benefits of Proper Tube Connections
Choosing the appropriate tube connection types provides numerous benefits, including:
- Increased Safety: Proper connections reduce the risk of leaks and system failures, enhancing overall safety.
- Improved Efficiency: Seamless connections ensure optimal flow rates, enhancing operational efficiency.
- Cost Savings: High-quality connections may reduce the need for frequent repairs and replacements.
Conclusion
Understanding the various tube connection types is essential for anyone involved in the design, implementation, or maintenance of piping systems. By choosing the right types of fittings and valves—such as those found at techtubes.in—you can ensure the durability and reliability of your systems. Always consider the requirements of your specific application and seek high-quality components that meet industry standards.
For more information on various tube fittings, ferrule fittings, and other products, visit techtubes.in and explore our comprehensive range of solutions. Optimizing your systems starts with understanding the right connections!