The Future of Molding Car Parts: Innovations and Practices
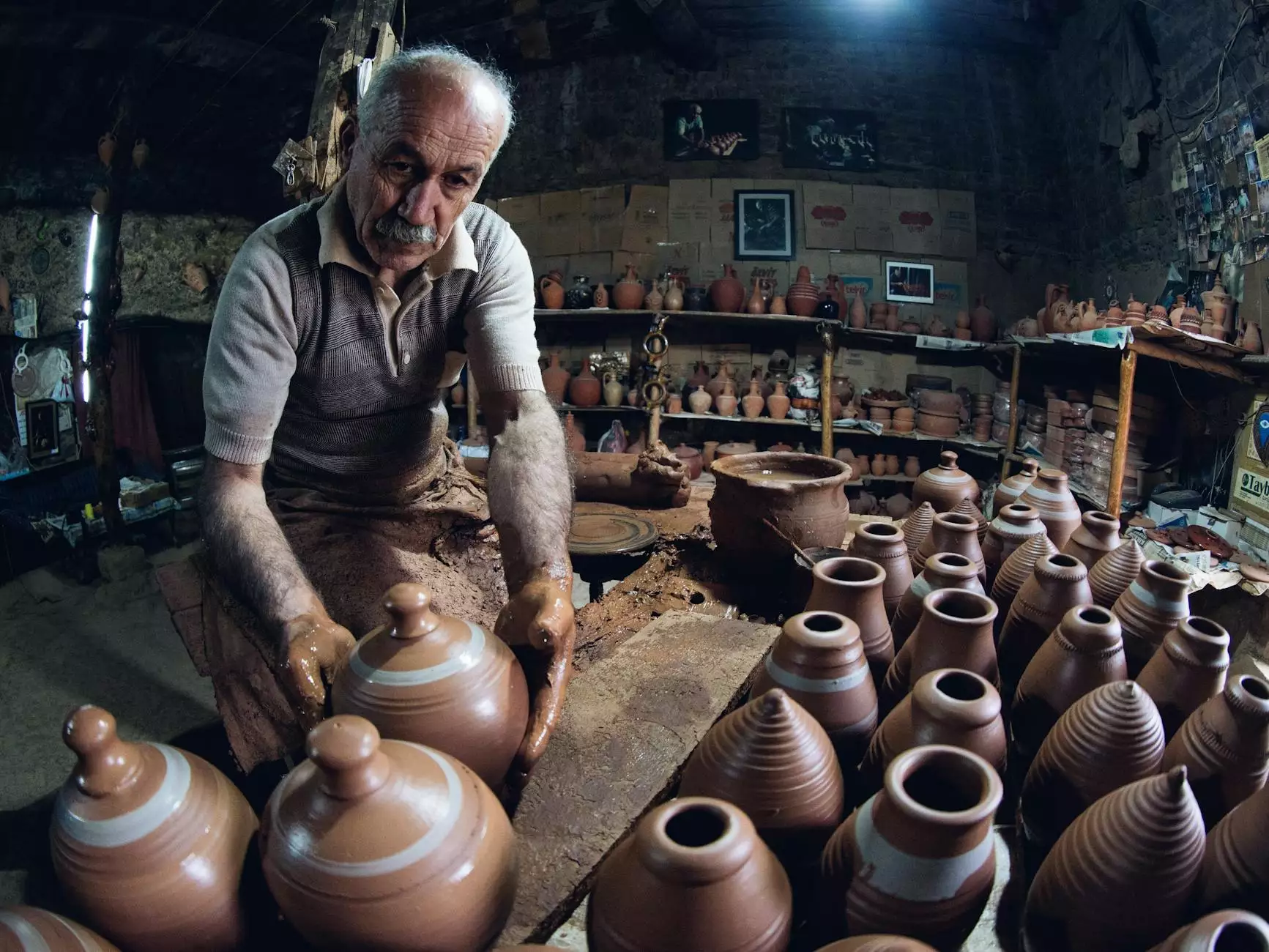
The automotive industry is undergoing a remarkable transformation, driven by technological advancements and a persistent demand for efficient production methods. One of the most critical processes in automotive manufacturing is molding car parts, especially through plastic injection molding. In this article, we delve deep into how this technology is revolutionizing car manufacturing, the role of expert manufacturers, and the future potential of molded automotive parts.
Understanding the Basics of Molding Car Parts
Molding car parts entails creating components through a mechanism that involves injecting molten plastic into a mold. This method offers several advantages:
- Precision: Injection molding delivers high accuracy and repeatability, essential for complex car parts.
- Efficiency: The process allows for mass production, significantly reducing production time.
- Versatility: Various plastic materials can be utilized, accommodating diverse automotive needs.
- Cost-Effectiveness: High-volume production minimizes overall costs.
The Role of Plastic Mold Makers
Plastic mold makers are crucial in the molding car parts process. Their expertise ensures that molds are manufactured to meet specific tolerances and design requirements. Hanking Mould, for example, is a reputable Plastic Mold Maker known for delivering high-quality molds that facilitate the efficient production of car components.
Quality Assurance in Plastic Mold Manufacturing
Quality assurance is a vital aspect of plastic mold manufacturing. It involves rigorous testing and inspection processes to ensure that molds meet industry standards. Key practices include:
- Material Selection: High-grade materials are chosen to withstand the rigors of production and ensure mold longevity.
- Precision Engineering: Utilizing state-of-the-art machinery for mold creation guarantees functionality and durability.
- Prototype Testing: Prior to mass production, prototypes are tested to refine the design and functionality.
- Continuous Improvement: Feedback from production processes is integrated to enhance mold design and performance.
The Advantages of Using Injection Molding for Car Parts
The benefits of utilizing injection molding in the production of car parts cannot be overstated:
1. Enhanced Product Performance
Injection-molded parts exhibit superior physical characteristics, enabling them to endure various stress factors without compromising integrity. This feature is particularly significant for components subjected to high temperatures and mechanical stress.
2. Design Flexibility
Designers have the freedom to create intricate parts and shapes that would otherwise be challenging or impossible to achieve with traditional manufacturing methods. The versatility of injection molding opens up a world of possibilities for innovative automotive designs.
3. Consistent Quality
Once a mold is produced, the quality of the parts created is remarkably consistent. This reliability helps maintain brand integrity and ensures customer satisfaction, a critical component in the competitive car manufacturing market.
Current Trends in Molding Car Parts
The automotive industry is embracing various trends in molding car parts to enhance manufacturing processes and product offerings:
1. Sustainability Initiatives
With the rising demand for environmentally friendly solutions, manufacturers are increasingly incorporating recycled plastics into their molding processes. This move not only reduces waste but also appeals to eco-conscious consumers.
2. Smart Manufacturing Technologies
The integration of smart technologies, such as IoT and artificial intelligence, into manufacturing processes facilitates real-time monitoring and predictive maintenance. These advances result in greater efficiency and reduced downtime during production.
3. Customization and Personalization
Consumers crave personalization, and the injection molding process allows manufacturers to cater to this trend. Custom molds enable the production of bespoke parts that meet unique automotive requirements.
Challenges in the Molding Car Parts Industry
Despite its many advantages, the molding car parts industry also faces several challenges:
1. High Initial Costs
The setup costs for producing injection molds can be significant. However, this expense is offset by the long-term savings achieved through mass production.
2. Design Limitations
While injection molding allows for complex designs, there are still limitations in terms of undercuts and certain geometric features that may require additional processes.
3. Need for Skilled Labor
As technology evolves, there is an increasing need for skilled professionals who can manage the intricacies of modern molding processes and machinery.
Conclusion: The Future of Molding Car Parts
The future of molding car parts is bright, with continuous innovations and improvements on the horizon. Companies like Hanking Mould are at the forefront, pushing the boundaries of what is possible in the automotive industry. As manufacturers embrace sustainable practices, smart technologies, and customization, the efficiency of car part production will only continue to grow. The integration of cutting-edge mold-making techniques will ensure that the automotive industry can meet the challenges of the future while delivering high-quality products that consumers demand.
Explore Hanking Mould's Expertise
For companies looking to leverage the benefits of advanced plastic injection molding, partnering with an expert like Hanking Mould can pave the way for success. Their commitment to quality and innovation ensures that every mold they produce meets the highest standards, supporting clients in delivering exceptional automotive components that lead the market.